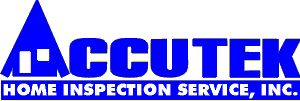
Contents:
Back
to Library > Back
Home

When you hear of roof leaks, your first thought is probably directed
to the roof covering, such as the asphalt shingles. You may be surprised
to hear that approximately 60 percent of all leaks occur at joints,
valleys, or projections through the roof.
Typical leak locations are at chimneys, plumbing vents, roof valleys,
dormers, joints where a roof meets a wall, skylights, and parapet
walls. In short, any time you have a roof penetration or projection,
you have a more vulnerable area.
Of the remaining 40 percent of roofing problems, approximately
25 percent of roofing failures are due to worn, deteriorated roofing
materials. The remaining 15 percent is due to improper roofing material
applications, poor workmanship and miscellaneous items.
The remedy for most problem areas is properly installed flashings.
Step flashings are typically aluminum :L-shaped" pieces used
to divert water away from the profjection or roof penetration. Proper
flashings and workmanship should develop a condition where the flashings
will be dependable for the life of the roof covering and beyond.
In most instances, proper flashings are made up of step and counter-step
flashings. The first piece on a step flashing is the "L-Shaped"
piece mentioned above. The average size is 7" long and 5"
wide. It is bent into the 7" length, with 3" and 2"
on each side. This step flashing is placed with the 3" side
against the roof shingles and the 2" side placed vertically
against the wall or chimney, etc.
The second piece, known as a counter flashing, covers the vertical
portion of the step flashing to keep water deflected away from the
top of the step flashing. At a wall, the siding will act as an appropriate
counter flashing. At a chimney, the counter flashing looks like
an inverted "L" with the short 3/4" portion being
inserted into the brick or masonry joints after the mortar has been
cut out.
Skylights should be installed on a curb to allow room for proper
flashing and should never be installed level at the roof surface.
The height of the curb is dictated by the slope of the roof (i.e.,
roofs with a slope of 4/12 to 6/12 should have a curb of at least
4"). Skylights on flat roofs should have a curb of 8"
or more depending on possible snow accumulation.
Roofs that do not allow water to drain successfully are prone to
problems at seams and premature deterioration. Ponding is generally
not considered accepatble if it does not evaporate within 48 hours
after a rain.
Problem areas should be addressed as soon as possible due to the
unavoiable interior damage that will typically occur (e.g., roof
sheathing, drywall or plaster and wood-framing components.)
Valleys are dependable if the proper materials are used and the
workmanship is acceptable. Valleys are vulnerable because a large
percentage of the water that hits the roof accumulates in the valleys.
This created a disproportionate amount of wear. It is not unusual
for the valleys to wear out ahead of the shingles.
Top
of Page

An asphalt shingle roof in good condition will keep your family
protected from water penetration, while a roof in poor or failing
condition can cause headaches and large bills due to damage and
urgency. Asphalt shingled roofs are by far the most common type
of roof covering found in homes today. They first came on the scene
in the early part of this century and quickly became the roof covering
of choice.
The condition of asphalt composition shingles is dictated by the
condition of the granules in the joints between the tabs or cutouts
in the shingles. Consider the following:
- If the granules are intact in the cutouts or joints between
the tabs, the shingles are acceptable and should have years of
remaining life.
- If the granules in the cutouts are worn and the asphalt matrix
is visible, the shingles are marginal because of the obvious wear
and limited remaining life expectancy, perhaps six months to two
years.
- If the granules and matrix in the cutouts are worn through and
you can see the shingles or sheathing below, the shingles are
no longer acceptable.
Curling or cupping shingles may be an indication of wear, age,
or condensation problems. However, it does not indicate failed shingles.
Remaining life expectancy could be two to five years.
Even when shingles are in poor condition, roofs with multiple layers
may not leak because of the layer of shingles below. These back-up
layers can deflect water to the gutter system.
The life expectancy of asphalt shingles is determined by the following:
- The slope of the roof. Shingles will last longer on higher sloped
roofs because water sheds quickly and more completely.
- The color of the roof. Lighter-color roofs last longer than
darker roofs because they reflect the sun better.
- Exposure to the sun. North-facing shingles last longer than
south-facing shingles because the sun causes as much damage as
rain and associated weather.
High-slope, light-color, east-west facing roofs can last 25 years
or more. Low-slope, dark-color, south-facing roofs may fail within
15 years. Roofs in the north tend to last longer than roofs in the
warmer, southern climates.
Careful attention should be given to flashings at all roof penetrations
and valleys. Proper flashings and valleys should control and divert
water away from the roof and walls of the house. The majority of
roofing problems come from these areas.
Top
of Page

Asphalt shingles are made of asphalt "flux," a material
which is refined from petroleum in the distillation process. Asphalt
flux is typically reinforced with glass fiber or cellulose fibers.
Glass fiber reinforcement has evolved as the most desirable choice.
The shingle matrix then receives a granular surface. Granules protect
the shingle from the sun and the weather and increase the fire-resistance
rating. Fiberglass-reinforced asphalt shingles typically have a
fire rating. However, the primary materials in the shingles are
cellulose and petroleum, which are flammable.
Shingles come in different shapes and configurations. The most
widely used shingles are self-sealing strip shingles. Asphalt shingles
are normally installed on roof slopes of four inches per foot or
more. On slopes of less than four inches per foot or where the January
mean temperature is 30 degrees F or less, the requirements are for
specific materials that are designed for low slopes. Asphalt composition
shingles were not designed for slopes of 4/12 or less.
Top
of Page

Skylights are great additions to a home. They add light and a contemporary
ambiance that's hard to match. When installed properly, they can
operate indefinitely and will need virtually no maintenance beyond
cleaning.
With the well-made units available today, the most common problem
with skylights is poor installation. If the skylight does not have
a manufactured or site-built "curb" (an elevated frame)
with proper step and counter flashings, you will probably have a
leaking skylight.
The recommended height of the curb will vary based on the type
and slope of the roof. If your roof has a steep slope, the curb
can be about 4" high. However, if your roof is flat, a curb
of not less than 8" is recommended. In colder climates, height
requirements should also accommodate the presence of snow on the
roof and its effect on the skylight. Snow on the south side of the
house melts faster than snow on the north side, due to the rotation
of the earth. Subsequently, skylights on the north side need to
be higher than on the south side because the snow lasts longer there.
It melts underneath the top layer of snow due to heat in the home,
yet is trapped by the top layer. This trapped water stands a better
chance of entering the skylight area than if it were on the south
side.
A counter flashing is an inverted L-shaped piece of metal that
goes under the skylight bubble or glass and covers the vertical
section of the step flashing. Its purpose is to divert the water
from the bubble to the step flashing. A step flashing is an Lshaped
piece of metal that goes under each course of shingles and goes
up the curb, or wall, of the skylight. Its purpose is to divert
the water away from the corner where the skylight and roof connect.
This is the same detail that is used successfully at chimneys, walls
and other roof projections.
Skylights come in different types, including wood, aluminum and
vinyl. They also come in a variety of sizes. The costs range significantly
based on the style of skylight you choose, as well as design of
the roof. For an average size skylight, perhaps 30" by 40",
you can spend as little as $150 for a plastic bubble to $850 or
more for a double-glass, motor-operated window with screen and blinds.
Installation is an additional expense. For a normal skylight installation,
fees will probably range between $300 and $500, depending on the
type of roof and skylight design. Look for a few professional carpenters
who are familiar with skylight installation to give you bids.
Before you decide on what type of skylight you want, consider the
purpose it will serve. If you just need additional light, you can
probably get away with a plastic bubble. If you are putting an office
in an attic with no windows, you may benefit greatly from a hand
crank or motorized model that will allow fresh air, as well as light,
to enter the space.

Back
to Library Back
Home Top
of Page
This site © 2010 Accutek Home Inspection Service,
Inc.
Internet Publishing and Hosting provided by GrapevineNetworks.com
Contact the webmaster with questions or comments.
|